【小規模食品工場向け】凝集加圧浮上 排水処理装置の日常点検|下水道放流基準を守り安定稼働へ(点検項目・日報ひな形付)
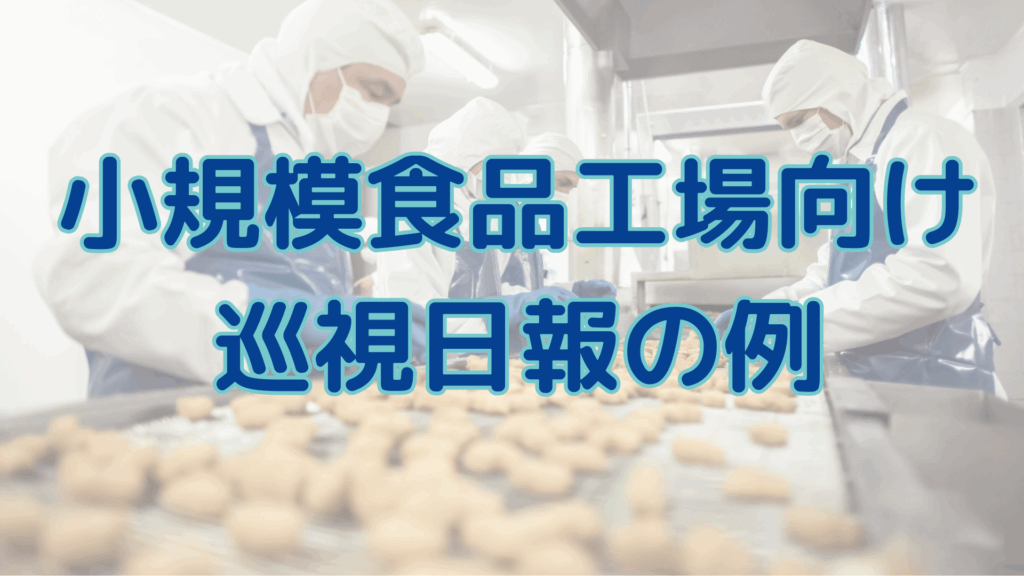
食品工場(惣菜、弁当、製菓、製パン、豆腐製造など)の運営において、排水処理は衛生管理や品質管理と並んで非常に重要な課題です。特に、下水道へ放流する場合、下水道法や自治体の条例で定められた排水基準(n-ヘキサン抽出物質、BOD、SSなど)を確実に遵守する必要があります。
基準超過は改善命令や罰則、場合によっては操業停止に繋がる可能性もあり、企業の信頼にも関わります。この排水基準遵守と安定した工場運営を支えるのが、日々の排水処理装置の日常点検です。
小規模&下水道放流の食品工場で多く採用されている凝集加圧浮上方式は、排水中の油分や固形物を効率的に除去する方法ですが、その性能を維持するためには適切な管理が不可欠です。
この記事では、小規模な食品工場で凝集加圧浮上方式の排水処理装置をお使いの担当者様に向けて、日常点検の重要性、具体的な点検項目とチェックポイント、そしてすぐに使える点検日報のひな形(例)を分かりやすく解説します。日々の排水管理業務の改善や、環境コンプライアンス体制強化の参考にしてください。
食品工場の排水処理、なぜ「日常点検」がこれほど重要なのか?
毎日の点検業務、その重要性を改めて考えてみましょう。食品工場の排水処理における日常点検が不可欠な理由は以下の通りです。
1. 排水基準(特に油分)の超過リスクを低減
食品工場排水の大きな特徴は油分(n-ヘキサン抽出物質)や固形物(SS)が多いことです。凝集加圧浮上装置はこれらを効果的に除去しますが、薬品注入量の不足、加圧ポンプやコンプレッサーの不調、スカム掻き寄せ不良などが起こると、処理能力が低下し、下水道放流基準を超過するリスクが高まります。日常点検で装置の健全性を確認することが、基準超過を防ぐための第一歩です。
2. 予期せぬ設備トラブルの防止と安定稼働
「ポンプからいつもと違う音がする」「圧力が不安定だ」「薬品の減りが早い」といった小さな変化は、設備トラブルの前兆です。日常点検でこれらを早期に発見し対処することで、突然の装置停止による生産への影響や、高額な緊急修理費の発生を防ぎ、排水処理設備の安定稼働に繋がります。
3. 処理コスト(薬品・電気・廃棄物)の最適化
日常点検を通じて、薬品(凝集剤など)の注入量が適切か、ポンプやコンプレッサーが効率的に稼働しているかなどを確認できます。過剰な薬品使用やエネルギーの無駄をなくし、また、適切に浮上分離されたスカム(汚泥)は含水率が比較的低いため、産業廃棄物処理コストの削減にも繋がる可能性があります。
4. 設備の維持管理と法令遵守の証明
日々の点検とメンテナンスは、排水処理装置の性能維持と長寿命化に不可欠です。また、点検日報として記録を残すことは、適正な排水管理を行っていることの証明となり、行政への報告や査察対応においても重要な資料となります。
凝集加圧浮上方式|仕組みと日常点検の重要ポイント
凝集加圧浮上方式の基本的な流れと、各工程での点検ポイントを解説します。(※貴社の設備構成に合わせてご確認ください)
原水槽(調整槽): 排水の入口をチェック
- 仕組み: 工場からの排水を受け入れ、一時的に貯留し、水質や流量の変動を均一化します。
- 点検ポイント: 水位、多量の油浮遊がないか、異臭、大きな固形物の混入がないか。
- 重要性: 後段の処理への負荷変動を抑え、油分が多い場合は前処理(グリストラップなど)の状況も確認します。
2. 凝集反応槽: 薬品反応の基礎を管理
- 仕組み: 凝集剤(PACなど)やpH調整剤(必要に応じて)を添加・混合し、排水中の微細な油分やSSをフロック(塊)にします。
- 点検ポイント: 攪拌機の作動状況、薬品注入ポンプの作動状況、薬品タンクの残量、フロックの形成状態(小さすぎないか、大きすぎないか)。
- 重要性:良好なフロック形成が、加圧浮上での除去効率を決定づけます。薬品注入量の調整や攪拌状態の確認が重要です。
3. 加圧ポンプ・加圧溶解タンク・コンプレッサー: 浮上分離の要
- 仕組み: 加圧ポンプで水を加圧溶解タンクへ送り、コンプレッサーからの圧縮空気と混合して、水中に空気を高圧で溶かし込みます(加圧水)。
- 点検ポイント: 加圧ポンプの作動音・振動・圧力、加圧溶解タンクの圧力計指示値、コンプレッサーの作動音・圧力。
- 重要性: 十分な圧力と空気量が確保されていることが、微細気泡を安定して発生させるために不可欠です。圧力不足や不安定さは浮上効率の低下を招きます。
4. 浮上分離槽: 汚れをまとめて浮かせて取る
- 仕組み: 加圧水を浮上槽内で減圧放出させ、発生した微細気泡をフロックに付着させて浮上させます。浮上したスカム(汚泥)はスキマーで掻き寄せられ、処理水は槽の下部から排出されます。
- 点検ポイント:
- スカムの浮上・掻き寄せ状況: 均一に浮上しているか、スキマーは正常にスカムを回収しているか。
- 処理水の透明度: 油分や濁りが十分に除去されているか。
- 微細気泡の発生状況: 槽全体に白濁するような細かい気泡が十分に出ているか。
- 重要性: この工程が油分・SS除去の心臓部です。処理水質を直接左右するため、目視での確認が非常に重要です。
5. 処理水槽/放流槽: 最終確認と放流
- 仕組み: 処理水を一時貯留し、下水道へ放流します。
- 点検ポイント: 処理水の外観(油膜、濁り)、pH(必要に応じて条例値と比較)、水位。
- 重要性:最終的な処理水質を確認し、下水道放流基準を満たしているかをチェックします。
6. その他(薬品タンク、ポンプ、計測機器): 装置全体の安定稼働を支える
- 点検ポイント: 薬品残量、漏洩の有無、ポンプの異音・振動、計器の指示値、センサーの汚れ
- 重要性: 薬品切れやポンプ故障は処理停止に直結。計測機器の精度維持も適切な水質管理の基礎となります。
実践!凝集加圧浮上用 点検日報ひな形(例)
日々の点検結果を確実に記録し、管理体制を強化するために、点検日報の活用は非常に有効です。以下に汎用的なひな形を示します。
排水処理装置 点検日報
点検日: ________年____月____日 (____曜日) 天候: ________ 点検者: ________ 印 確認者: ________ 印
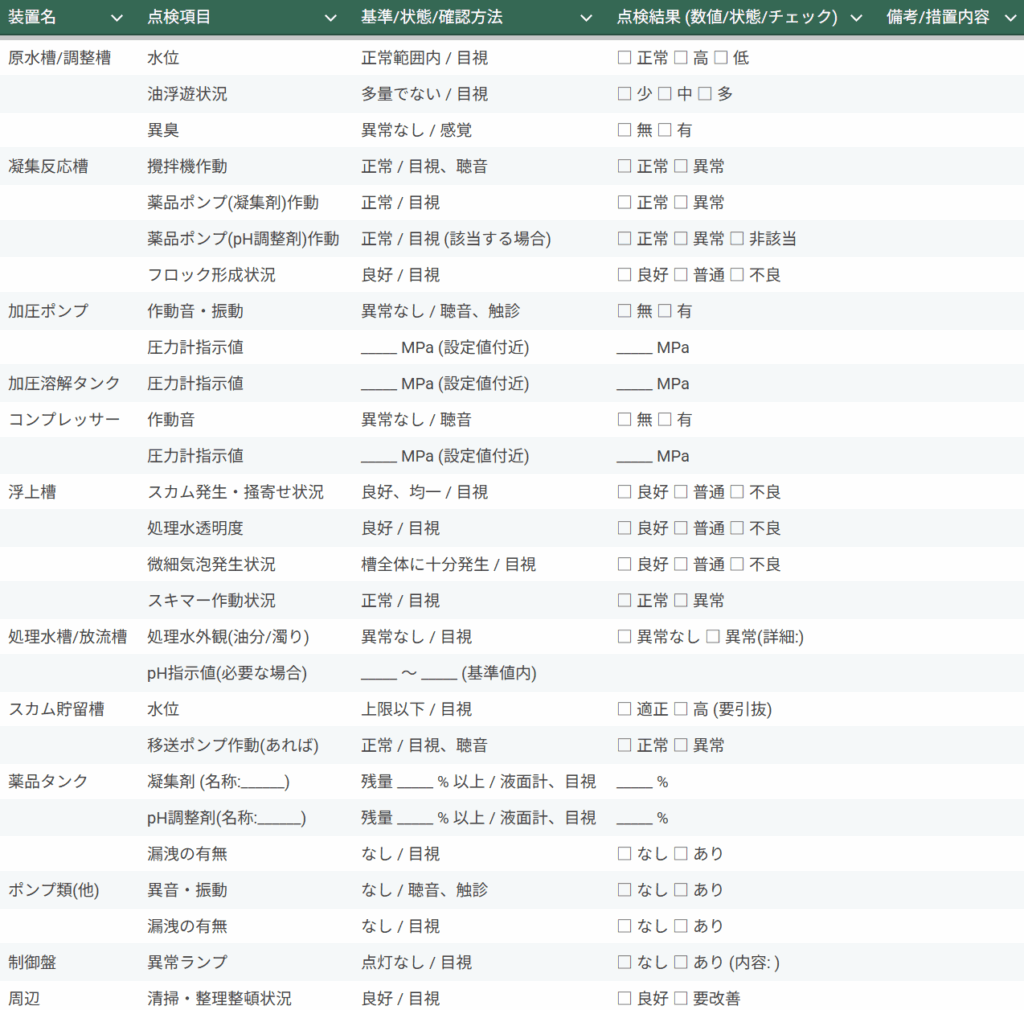
【重要】
- これはあくまで一例です。貴社の排水処理装置の構成や特徴に合わせて、項目を追加・削除・修正し、最適なフォーマットを作成してください。
- 基準値や設定範囲は、必ず自社の設備仕様や排水基準に基づいて具体的に記載しましょう。
- 記録は、単にチェックするだけでなく、異常があった場合の具体的な状況や実施した措置内容も詳しく記載することが重要です。これにより、後日の原因分析や再発防止に役立ちます。
点検をより効果的に行うためのヒント
最後に、日常点検を形骸化させず、より効果的に行うためのヒントをいくつかご紹介します。
- 五感をフル活用する: 計器の数値だけでなく、「いつもと違う音はしないか?」「変な臭いはしないか?」「ポンプの振動は大きくなっていないか?」など、五感を使って変化を捉えることが大切です。(※回転部への接触や感電には十分注意してください)
- 「正常な状態」を知る: 何をもって「異常」とするか判断するためには、まず「正常な状態」をしっかり把握しておく必要があります。普段の音、振動、色、臭い、計器の指示値などを意識して観察しましょう。
- 小さな変化も見逃さない: 「これくらい大丈夫だろう」という油断が、大きなトラブルを招くことがあります。少しでも気になる点があれば記録し、必要であれば上司や担当者に報告・相談する習慣をつけましょう。
- 記録を継続し、傾向を見る: 毎日記録を続けることで、単日の異常だけでなく、徐々に変化していく傾向(例:フィルター差圧が徐々に上昇している)を掴むことができます。これにより、計画的なメンテナンスが可能になります。
- チームで情報を共有する: 点検は一人で行う場合も多いですが、気づいたことや異常時の対応などをチーム内で確実に共有・引継ぎすることが重要です。報告・連絡・相談の体制を整えておきましょう。
なかなか日報データを活かせない時は、、、
ウォーターデジタル社では、新サービス「撮るだけ点検日報」を提供しています。この機会に簡単にデジタルデータ化が可能になる本サービスの検討は如何でしょうか?
まとめ
食品工場における凝集加圧浮上方式の排水処理装置の日常点検は、下水道放流基準を遵守し、安定した工場運営を継続するための生命線です。日々の地道なチェックが、水質汚濁のリスクを低減し、設備の安定稼働、ひいてはコスト削減と企業の信頼維持に繋がります。
日々の地道なチェックが、未来の大きなトラブルを防ぎます。この記事を参考に、ぜひ自社の点検体制を見直し、より確実で効果的な日常点検を実践していきましょう。それが、持続可能な工場運営への確かな一歩となるはずです。
また、必要に応じで、専門業者や社内の有識者/経験者に話を聞いて、よりよい日報作成および向上を図っていきましょう。
専門業者が周りにいない時や、第三者の意見を聞きたいときは、水廻りのセカンドオピニオンであるウォーターデジタル社にぜひお問い合わせください。